Finishes
Finishing is a crucial stage in the production of quality products. Siderpali uses two
processes, varnishing and galvanizing, to ensure resistance and durability to its
products.
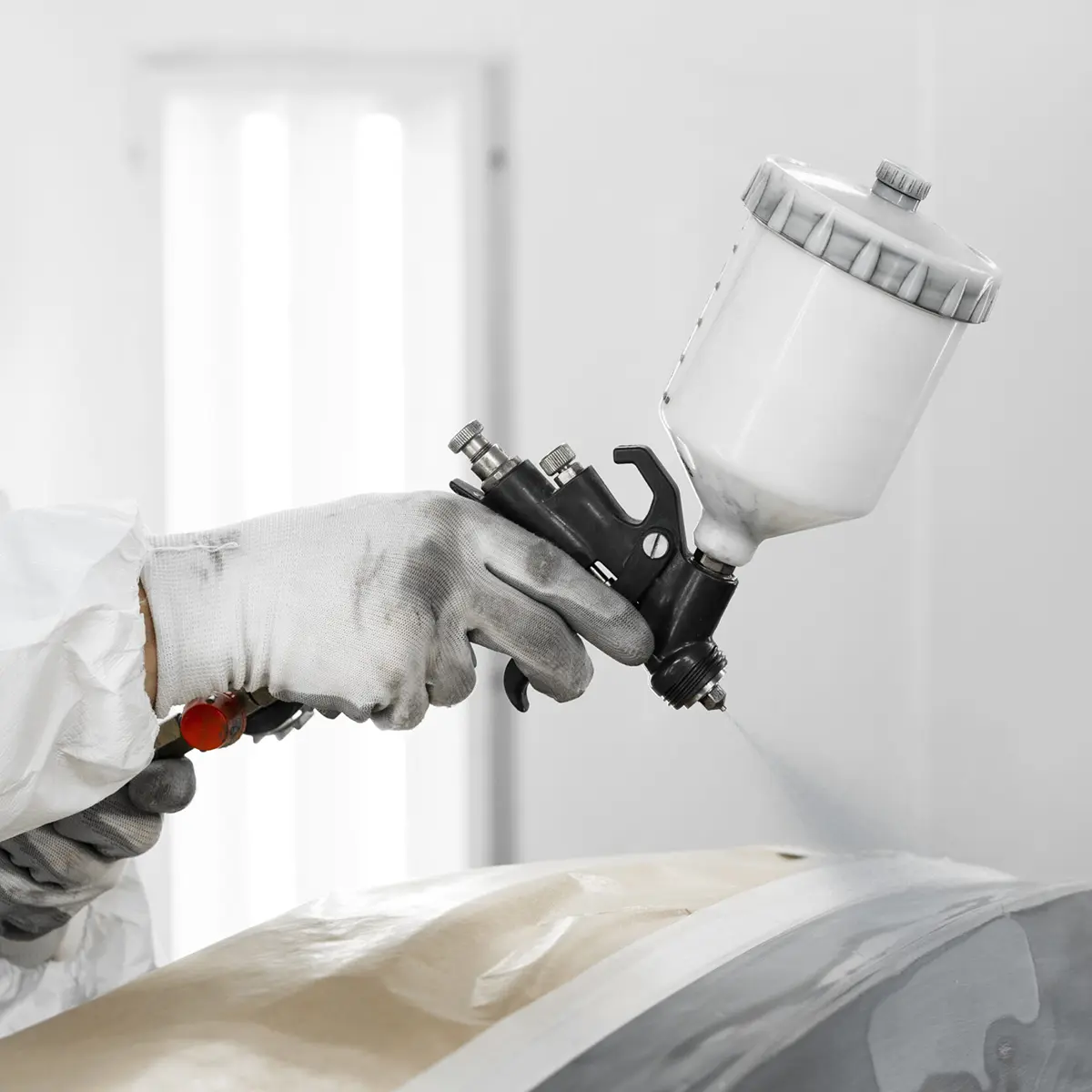
PAINTING
a powder with primer bottom cycle machining
Pre-treatment (phospho decapage)
Degreasing treatment based on orthophosphoric acid containing aqueous solutions delivered through spray nozzle ramps at 50° c.
Rinse
Double wash to remove residues from the previous treatment, first with mains water and then with demineralized water. The solutions are sprayed on the products by nozzle ramps inside a tunnel.
Drying
The articles are placed in a hot-air drying oven at a temperature of 140°C, so that the pieces are perfectly dry before moving to the dust deposition stage.
Powder application
Dust (of the required color) is applied to the articles by electrodeposition. All this is done in an automated cabin with automatic reciprocators and workstations for manual adjustments. The powders applied are of the polyester type with the possibility of smooth and wrinkled finishes. Powders of the interpon d94 hr gloss akzo nobel series are used, specific for architecture and free from heavy metals “tgic free”.
Polymerization (cooking)
The dust deposition phase is followed by cooking in a hot air oven at a variable temperature of 170-200 °c. At this stage, the material is left in the oven for the time necessary for the polymerization of the powder.
Unloading and monitoring
When the materials are removed from the transport equipment, a visual check is carried out to ensure that the poles do not have surface defects such as open areas (free of paint), bubbles or craters that impair the correct use of the poles. The final check of the coating thickness by the magnetic method is followed.
Preparing Surfaces
Clean with manual tools (scrapers, brushes, etc.) or automatic tools, until the clumps, cracks, dripping and white salts (oxide) are completely removed. Surfaces should be washed with non-chlorinated solvents in order to remove fats, oils, salts and contaminants in general, resulting from the galvanizing process.
Phos Phosphorus fat
Use a solution with a constant temperature of 40-50°C based on orthophosphoric acid, titanium salts and additives with suitable surfactants. Purpose: to remove the residues of oils and fats from the surfaces by chemically converting the surface layer favoring the formation of salts phosphates which ensures the clinging of the paint.
Pickling and washing
Use a solution with a constant temperature of 40-50°C based on phosphoric acid, titanium salts and additives with suitable surfactants.
Wash with mains water at room temperature to remove excess residue from previous treatments. Purpose: to remove the residues of zinc oils, fats and oxides from the surfaces; to exert a stripping and mordant action on the surfaces and to chemically convert the surface layer favoring the formation of salts-phosphates which ensures the clinging of the paint.
Zirconization
Constant temperature conversion of 45°C
Washing
Application of primer powder before painting phase. The product that is used is able to create a strong protective barrier against the corrosive action of natural and chemical agents even in highly aggressive environments, it will guarantee a long life of the painted item.
Painting
Dust settling on the test pieces.
Polymerization
Oven temperature: constant at 190°C with Δt +/- 10°C for 25 to 40 minutes depending on the thickness of the painted metal.